SCARA Robots: The Ultimate Guide to Selective Compliance Automation for Industry 4.0
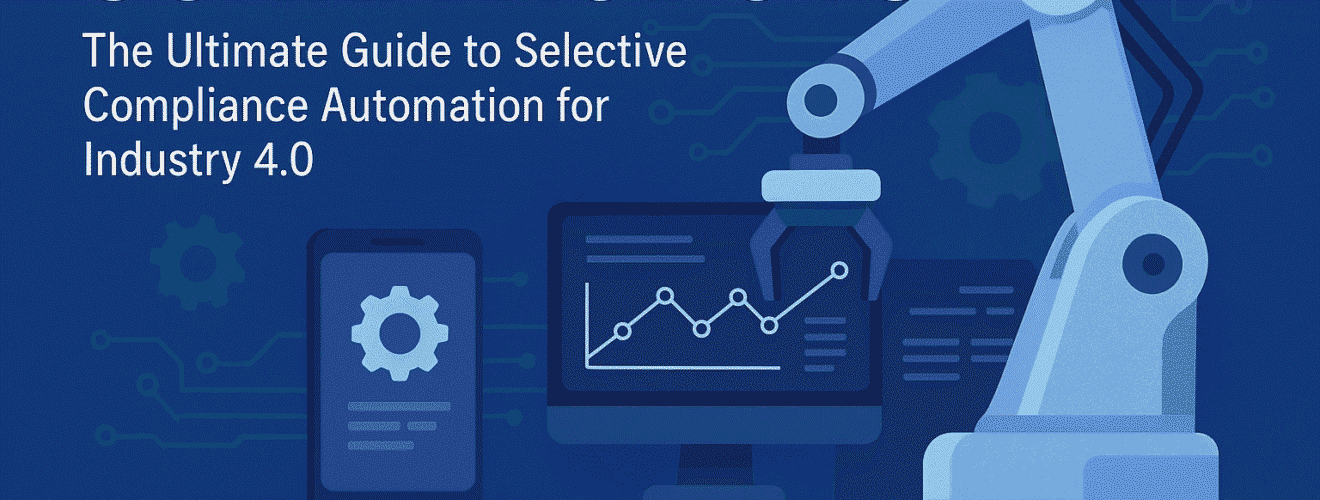
Imagine a robotic arm that can place hundreds of components per minute with micron-level precision—without ever getting tired or making a mistake.
In high-speed production environments, every millisecond counts. Traditional automation systems, though reliable, often struggle to meet the precision, flexibility, and speed required in modern industries like electronics, pharmaceuticals, and advanced packaging. This is where SCARA robots come into play.
Short for Selective Compliance Assembly Robot Arm, SCARA robots are built specifically for high-speed, horizontal movement tasks with incredible accuracy. From placing tiny electronic components on PCBs to assembling medical devices in sterile environments, SCARA robots have become a staple of Industry 4.0 automation.
In this detailed guide, you’ll learn:
- What SCARA robots are and how they function
- Why they outperform other robotic arms in specific applications
- Where they are used and how to select the right model for your plant
- Real-world examples of SCARA implementation and ROI
Whether you’re an engineer evaluating automation solutions or a plant manager exploring smart manufacturing, this blog will equip you with actionable insights on how SCARA robots can transform your operations.
Table of Contents
What Are SCARA Robots?
SCARA stands for Selective Compliance Assembly Robot Arm. It refers to a 4-axis industrial robot designed primarily for horizontal pick-and-place, assembly, and high-speed automation tasks.
Unlike 6-axis articulated robots that offer full flexibility in 3D space, SCARA robots are purposefully constrained. Their structure allows compliance—or flexibility—in the X-Y plane, but rigidity in the Z-axis (vertical direction). This makes them exceptionally well-suited for tasks like:
- Inserting components into PCBs
- Moving parts between conveyor stations
- High-speed screwdriving or gluing
- Packaging lightweight items
Key Characteristics:
- 4 Degrees of Freedom (DOF):
- Joint 1: Base rotation
- Joint 2: Elbow swing
- Joint 3: Vertical Z-axis motion
- Joint 4: End-effector rotation (θ-axis)
- High repeatability: Typically in the range of ±0.01 mm
- Compact footprint: Can be mounted on a table or inside an enclosed workstation
- Fast cycle times: Capable of 0.3–0.5 seconds per pick-and-place cycle depending on payload
Think of a SCARA robot as a robotic version of a human arm resting on a table: it can swing side-to-side and move up and down, but it doesn’t need to reach overhead or rotate its wrist in all directions. That limited but intentionally designed movement is what gives SCARA its speed, precision, and cost efficiency.
In short, SCARA robots fill the sweet spot between low-flexibility Cartesian robots and expensive, fully articulated 6-axis arms—making them ideal for repetitive, high-speed tasks in confined spaces.
How SCARA Robots Work: Mechanism and Motion
To understand why SCARA robots are so effective in high-speed industrial applications, you need to look at how they’re built—and how their design directly supports their performance.
SCARA robots operate using a four-axis mechanical structure, built to replicate the motion of a human arm on a horizontal plane, with limited but precise vertical movement.
Mechanical Structure of a SCARA Robot
A typical SCARA robot consists of:
- Base (Fixed Column):
Anchors the robot to a surface and contains the control housing. - Rotary Arm 1 (Shoulder):
Connected to the base and rotates horizontally. - Rotary Arm 2 (Elbow):
Hinged to Arm 1, provides additional reach through a second horizontal rotation. - Vertical Z-Axis Slide:
Provides up-and-down motion for inserting, picking, or placing objects. - Rotary Theta Axis (End Effector Rotation):
Rotates the gripper or tool attached at the end for alignment tasks like fastening or positioning.
Working Principle: Selective Compliance
The term “Selective Compliance” is key.
SCARA robots are:
- Compliant (flexible) in the X-Y plane, allowing them to move sideways and forward/backward with speed and precision.
- Rigid (non-compliant) in the Z-axis, making them ideal for vertical insertions like placing pins into holes or dropping components into trays.
This selective compliance reduces the risk of damage during insertion tasks and helps the robot absorb minor horizontal misalignments without exerting force on delicate parts—a major advantage in electronics or precision assembly lines.
Motion Profile: Smooth, Fast, Repeatable
SCARA robots follow a very specific motion pattern:
- Rotate Arm 1 (Base Joint): Sweeps the entire arm outward.
- Swing Arm 2 (Elbow): Extends or retracts reach across the X-Y plane.
- Lower or Raise Z-Axis: Engages with the part or surface vertically.
- Rotate Theta Axis: Aligns the part as needed (e.g., for screw orientation).
Cycle times can be as low as 0.3 seconds depending on the application, payload, and travel distance—making SCARA one of the fastest robot types available for short-distance horizontal tasks.
🧠 Real-World Analogy
Think of a SCARA robot like your own arm on a table:
- Your shoulder joint moves your arm left and right
- Your elbow helps extend your reach
- Your hand moves up and down to pick or place items
- Your wrist turns to align the item properly
Now imagine doing this 100 times per minute, with perfect accuracy every time—that’s what a SCARA robot is built to do.
Advantages of SCARA Robots
When it comes to tasks that demand speed, precision, and simplicity, SCARA robots consistently outperform many other types of automation systems. Their specialized design, limited axis movement, and high repeatability make them especially efficient in repetitive, horizontal plane operations.
Let’s explore the core advantages of SCARA robots—and why manufacturers across sectors are integrating them into modern production lines.
1. High-Speed Operation
SCARA robots are built for rapid, short-distance movement. Thanks to their lightweight arms and limited axis design, they can complete pick-and-place cycles in 0.3–0.5 seconds, which is significantly faster than most 6-axis articulated robots.
Use Case: In electronics assembly, SCARA robots are used to place tiny components at high speed without compromising accuracy.
2. Exceptional Repeatability and Accuracy
Repeatability is critical for tasks like component insertion, screwdriving, or adhesive dispensing. SCARA robots offer ±0.01 mm to ±0.02 mm repeatability, making them ideal for precision assembly in medical devices, PCBs, and sensor systems.
Why It Works: Rigid Z-axis ensures accurate vertical movement, while selective compliance absorbs minor misalignments in X-Y.
3. Compact and Space-Efficient Design
Unlike bulky Cartesian setups or large 6-axis robots, SCARA robots have a small footprint. Their arms fold neatly within their working envelope, allowing them to fit into tight enclosures, small cells, or tabletop workstations.
Ideal For: Cleanroom environments, modular conveyor lines, and space-constrained factory floors.
4. Lower Cost and Maintenance
Fewer moving parts and simpler kinematics translate to:
- Lower upfront costs than 6-axis or Delta robots
- Simpler maintenance schedules
- Reduced risk of mechanical failure
Bonus: Many SCARA robots come pre-integrated with controllers, making them plug-and-play for integrators and OEMs.
5. Easy Integration with Vision and Conveyors
SCARA robots can be seamlessly integrated with:
- Machine vision systems for alignment and inspection
- Conveyor tracking for dynamic part picking
- Part feeders, trays, and sensors for precise in-feed coordination
Result: A smooth, synchronized workflow that enhances throughput without increasing manpower.
6. Ideal for Horizontal Assembly and Insertion Tasks
Selective compliance in the X-Y direction makes SCARA robots uniquely suited for:
- Press-fitting
- Component insertion
- Peg-in-hole operations
This flexibility allows the robot to naturally correct slight misalignments during horizontal insertions—reducing breakage, stress, and rework.
Summary Table: SCARA Robot Advantages
Feature | Advantage |
---|---|
Selective compliance | Absorbs X-Y misalignment in insertion tasks |
Fast cycle times | Enhances production throughput |
High repeatability | Perfect for precision assembly |
Compact footprint | Saves valuable floor space |
Simple 4-axis design | Lower maintenance and integration costs |
Easy peripheral integration | Works well with vision, conveyors, feeders |
SCARA Robot Applications in Industry
SCARA robots are widely deployed in industries that require fast, precise, repetitive operations on a horizontal plane. Their versatility, compactness, and reliability make them a preferred choice for assembly lines, cleanrooms, packaging zones, and precision placement tasks.
Let’s explore the most common industries and how SCARA robots are used in each.
1. Electronics Manufacturing
SCARA robots are almost synonymous with high-speed electronics assembly.
Applications:
- Placing capacitors, resistors, and ICs on printed circuit boards (PCBs)
- Soldering operations with automated precision
- Handling delicate components for smartphones, tablets, and wearables
- Screw tightening for casings or enclosures
- Dispensing adhesives or thermal compounds
Why SCARA? Their speed, accuracy, and compact design make them ideal for densely packed production cells and sensitive component handling.
2. Medical and Pharmaceutical Industries
In sterile and contamination-sensitive environments, SCARA robots support precise, contact-free operations.
Applications:
- Handling test tubes and vials
- Assembling syringes or diagnostic devices
- Packaging blister packs and cartons
- Dosing and sealing small medical containers
Why SCARA? Cleanroom compatibility, high accuracy, and smooth operation reduce contamination risk while ensuring compliance with strict quality norms.
3. Automotive Component Assembly
While 6-axis robots dominate heavy lifting in automotive plants, SCARA robots excel in sub-assembly zones.
Applications:
- Sensor and microcontroller assembly
- Screw insertion in dashboards or control panels
- Gluing/sealing delicate parts
- Pick-and-place for lightweight brackets and clips
Why SCARA? Their selective compliance ensures proper insertion of delicate, precision-fit components that might otherwise break under rigid motion.
4. Consumer Goods and Appliance Assembly
Consumer electronics, personal care devices, and small appliances are often assembled on semi-automated lines—where SCARA robots are highly effective.
Applications:
- Inserting batteries, labels, or components
- Capping and closing
- Product handling during packaging
- Flexible tray loading and unloading
Why SCARA? They can handle small products at a high rate while adapting to product design changes with minimal reprogramming.
5. Food and Beverage Packaging
SCARA robots are increasingly used in hygienic environments for high-speed, lightweight packaging tasks.
Applications:
- Sorting and placing chocolates, snack bars, or bottled items
- Tray loading and unloading
- Handling primary or secondary packaging in sanitized zones
Why SCARA? Many models meet IP-rated washdown or cleanroom standards, making them suitable for food-grade operations.
6. Logistics and Small-Scale Warehousing
In e-commerce, pharma warehousing, and micro-fulfillment centers, SCARA robots assist in fast-paced sorting and movement.
Applications:
- Item sorting into bins
- Label application
- Handling light SKUs in packaging cells
- Part movement between AGVs or conveyor belts
Why SCARA? Their speed and ability to perform repetitive actions continuously make them ideal for high-throughput, low-payload environments.
SCARA Robots vs Other Industrial Robots
Every type of industrial robot has its strengths. Choosing the right one depends on your task requirements—speed, range of motion, precision, payload, space, and cost. SCARA robots shine in specific use cases, but how do they stack up against others?
Let’s break it down with a detailed comparison.
SCARA vs Delta Robots
Feature | SCARA Robot | Delta Robot |
---|---|---|
Axes | 4 | 3–4 |
Speed | Very High (0.3–0.5s cycles) | Extremely High (even faster) |
Motion Plane | Horizontal (X-Y-Z + rotation) | Typically vertical dome (X-Y-Z) |
Payload | Light to Medium (up to 20 kg) | Light (up to 5 kg) |
Flexibility | Moderate | Limited |
Use Cases | Insertion, pick & place, assembly | Ultra-fast pick-and-place |
Ideal For | Assembly lines, insertion tasks | Lightweight food, pharma items |
Verdict: Choose SCARA for insertion/assembly tasks. Choose Delta if you need ultra-fast, lightweight sorting.
SCARA vs 6-Axis Robots
Feature | SCARA Robot | 6-Axis Robot |
---|---|---|
Axes | 4 | 6 |
Flexibility | Moderate (2D + vertical motion) | Full 3D articulation |
Speed | Very High | Moderate to High |
Payload | Light to Medium | Medium to Heavy |
Complexity | Simple | Complex programming |
Cost | Medium | High |
Use Cases | Fast planar operations | Welding, painting, complex handling |
Verdict: Choose SCARA for high-speed, low-complexity tasks. Choose 6-axis for flexibility and multi-directional tasks.
SCARA vs Cartesian Robots
Feature | SCARA Robot | Cartesian Robot |
---|---|---|
Axes | 4 (rotational) | 3–4 (linear) |
Speed | Very High | Medium |
Footprint | Compact | Large |
Cost | Moderate | Low |
Flexibility | Higher (rotation included) | Lower (only straight-line motion) |
Use Cases | High-speed pick-and-place, assembly | Basic positioning, heavy lifting |
Verdict: Choose SCARA for faster and more dynamic motion. Choose Cartesian for low-cost, heavy-duty, linear tasks.
Summary Table: When to Choose SCARA Robots
Task Type | Best Robot Type | Why SCARA Works Well |
---|---|---|
PCB Assembly | SCARA | Speed, accuracy, compact design |
Ultra-fast food packaging | Delta | Speed > precision |
Complex welding/painting | 6-Axis | Full 3D movement required |
Labeling/light packaging | SCARA | Precise, repeatable movement |
Heavy linear motion | Cartesian | Strong, cost-effective |
By understanding these differences, manufacturers can select the robot that offers the right balance of cost, performance, and capabilities for their specific process.
Limitations of SCARA Robots
While SCARA robots are extremely effective for specific tasks, they’re not universal solutions. Understanding where they don’t fit is just as important as knowing where they shine.
Here are the primary limitations of SCARA robots:
1. Limited Range of Motion (4 Axes Only)
SCARA robots are confined to:
- Rotational movement in the horizontal plane (X-Y)
- Limited Z-axis motion (vertical)
- Minimal rotation (θ-axis) of the end effector
Limitation: They cannot perform complex 3D or angled movements, which are often required in welding, painting, or multi-surface assembly.
2. Not Ideal for Large or Heavy Payloads
While SCARA robots are fast and precise, they are best suited for light to medium loads (typically up to 20 kg, depending on the model).
Limitation: For heavy lifting, long-reach applications, or handling bulky items, Cartesian or 6-axis robots are more appropriate.
3. Limited Working Envelope
SCARA robots operate best within a defined circular or semi-circular area in the horizontal plane. Their reach is fixed and constrained by the arm length and base mount.
Limitation: In applications that demand larger travel distances or multiple-level workspace access, SCARA robots fall short.
4. Not Suitable for Complex Part Orientations
SCARA’s end effector has only one axis of rotation, making it challenging to:
- Flip parts
- Handle orientation-sensitive assembly
- Perform contour tracking or polishing tasks
Limitation: For dynamic or multi-orientation handling, 6-axis articulated robots are more effective.
5. Floor Mounting Constraints
Most SCARA robots are mounted on fixed surfaces like tables, frames, or enclosures. They may not adapt easily to ceiling or wall mounts.
Limitation: Flexibility in robot placement is limited compared to some 6-axis or Delta robots designed for inverted mounting.
Summary Table: SCARA Robot Limitations
Limitation | Description | Better Alternative |
---|---|---|
Limited axes (no full 3D movement) | Cannot tilt or articulate in all directions | 6-axis robot |
Restricted payload capacity | Not for heavy or bulky parts | Cartesian, 6-axis |
Fixed working radius | Short-range operations only | Gantry, mobile robots |
Limited part orientation handling | No dual-axis wrist rotation | Articulated robot arm |
Mounting flexibility | Mostly fixed/table-mounted | Delta or 6-axis (ceiling) |
Understanding these limitations ensures that SCARA robots are deployed only where they truly outperform—high-speed, high-precision, repetitive tasks on a horizontal plane.
How to Select the Right SCARA Robot
Choosing the right SCARA robot isn’t just about picking a model with the highest speed or smallest footprint. It’s about aligning the robot’s capabilities with your specific production goals, environmental conditions, and integration setup.
Here are the key factors to evaluate before selecting a SCARA robot:
1. Payload Capacity
Definition: The total weight the robot can handle, including grippers, tools, and the workpiece.
Tip: Always calculate the combined weight of the end effector + part + any vacuum or tool changer.
Rule of Thumb:
Choose a robot with 20–30% more payload capacity than your heaviest part to avoid performance drops and long-term wear.
2. Reach and Working Envelope
Definition: The horizontal distance the robot can cover from its base to the furthest operational point.
Common Reach Ranges: 150 mm to 1000 mm (based on arm length)
Tip: Map your layout and ensure all stations (pick, place, reject bin) fall within this radius.
3. Cycle Time Requirements
Definition: The time the robot takes to complete one full pick-and-place or assembly cycle.
Typical SCARA Cycle Times:
0.3–0.5 seconds (no-load)
0.6–1.2 seconds (with payload)
Tip: For high-speed lines like PCB placement or cosmetics packaging, prioritize SCARA models with sub-0.5 sec cycle ratings.
4. Repeatability and Precision
Definition: How accurately the robot returns to the same point each time.
Standard Tolerance: ±0.01 mm to ±0.02 mm
Use Cases Requiring High Repeatability:
- Electronics
- Medical device assembly
- Optical component alignment
5. End Effector Compatibility
Consider:
- Gripper type (pneumatic, electric, magnetic, vacuum)
- Tool weight and dimensions
- Tool center point (TCP) calibration support
Tip: Choose a robot with IO and communication support for your specific gripper or tool control system.
6. Vision System and Conveyor Tracking
If you’re handling dynamic parts:
- Check for camera integration compatibility
- Verify real-time conveyor tracking features
- Ensure the robot supports external vision software (e.g., Cognex, Keyence)
7. Mounting and Environmental Ratings
- Will the robot operate in a cleanroom or washdown zone?
- Does it need dust-proofing (IP rating)?
- Is ceiling or wall mounting required for your layout?
Look for: IP-rated SCARA models with ISO class certification for pharma or food applications.
8. Communication and Control Interface
Ensure compatibility with:
- Your PLC or SCADA system
- HMI dashboards
- Industry-standard protocols (Ethernet/IP, Modbus, PROFINET, etc.)
Why It Matters: Faster integration = lower downtime during commissioning.
9. Software and Programming
Evaluate:
- Ease of use of the programming environment
- Simulation support
- Pre-programmed templates or teach-by-demonstration options
For first-time users: Opt for a vendor offering intuitive drag-and-drop software or graphical programming tools.
10. After-Sales Support and Training
Before finalizing a vendor, ask:
- Do they offer installation, calibration, and staff training?
- Is remote diagnostics supported?
- What’s the average response time for technical support?
Tip: A great robot with poor support is a long-term liability. Always verify service network coverage in your region.
Suggested Brands and Models
Brand | Notable SCARA Models | Known For |
---|---|---|
Epson | LS-Series, T-Series | Cost-effective, compact, fast |
Yamaha | YK-XG Series | High rigidity, precision |
Omron | i4L and i4H SCARA | EtherCAT integration, compact build |
Stäubli | TS2 SCARA | Cleanroom-ready, pharma-focused |
Fanuc | SR-3iA, SR-6iA | User-friendly, versatile |
SCARA Robots in Industry 4.0 and Smart Manufacturing
Industry 4.0 is not just a buzzword—it’s a real, measurable shift in how modern factories operate. At the center of this transformation are smart machines that communicate, adapt, and improve without human intervention. SCARA robots play a vital role in this evolution by offering fast, connected, and data-driven automation.
Here’s how SCARA robots contribute to smart manufacturing and Industry 4.0 ecosystems:
1. Seamless Integration with IoT and MES Systems
Modern SCARA robots can be connected directly to:
- IoT platforms that track cycle time, part counts, energy use, and fault alerts
- Manufacturing Execution Systems (MES) that oversee production lines in real-time
- Cloud dashboards for centralized monitoring and diagnostics across multiple locations
Benefit: Plant managers get real-time visibility into robot performance, efficiency, and predictive maintenance needs—accessible from any location.
2. Real-Time Performance Monitoring and Analytics
Smart SCARA robots provide continuous data streams:
- Throughput per minute/hour
- Number of completed pick-and-place cycles
- Alarm frequency and causes
- Idle time vs. active time
This data feeds into KPIs like:
- OEE (Overall Equipment Effectiveness)
- Cycle consistency
- Uptime/downtime ratios
- Preventive maintenance triggers
Result: Data-backed decisions for optimizing productivity and reducing operational bottlenecks.
3. Remote Diagnostics and Predictive Maintenance
With remote access tools and connected PLCs, service teams or in-house engineers can:
- Diagnose faults remotely
- Update programs or logic from offsite
- Schedule maintenance before failures occur
Example: A drop in arm speed or slight misalignment in pick location can trigger alerts before it impacts output—minimizing unplanned downtime.
4. Interoperability with Other Smart Equipment
SCARA robots can be synchronized with:
- Smart conveyors that vary speed based on load
- Machine vision systems with AI-driven part recognition
- Automated packaging machines or labelers
- AGVs and AMRs (Automated Guided Vehicles or Mobile Robots) in warehouses
Use Case: A SCARA robot picks components off a conveyor tracked by a vision camera, places them in packaging cells, and signals an AGV when the tray is full.
5. Role in Lights-Out Manufacturing
In advanced factories, SCARA robots are part of unmanned, 24/7 operations, where machines run with little to no human intervention.
Why SCARA is ideal for lights-out:
- High reliability and repeatability
- Lower maintenance needs compared to articulated robots
- Remote alert and restart capabilities
- Compact footprint for high-density cell setups
Summary: SCARA Robots in Industry 4.0
Industry 4.0 Feature | SCARA Robot Capability |
---|---|
IoT connectivity | Real-time data, cloud access |
Smart analytics | Cycle time, part count, alarm tracking |
Remote diagnostics | Predictive maintenance and alerts |
Inter-device communication | Syncs with vision, conveyors, AGVs |
Automation continuity | Supports 24/7 operation |
SCARA robots aren’t just automation tools—they’re smart, connected assets that drive productivity, visibility, and flexibility in Industry 4.0-ready plants.
s After 3 Months
Metric | Before Automation | After SCARA Deployment |
---|---|---|
Component misalignment rate | 3.4% | 0.6% |
Manual rework time/month | 110 hours | 18 hours |
Labor cost per shift | ₹4,500 | ₹2,000 (one operator needed) |
Output per hour | 180 units | 235 units (30% increase) |
ROI Payback Period | — | < 14 months |
Additional Benefits
- Improved inspection pass rate, reducing bottlenecks at AOI stations
- Stable production during night shifts due to automated operation
- Lower reject ratio, contributing to higher customer satisfaction and fewer warranty claims
This case clearly shows how SCARA robots—when deployed strategically—can deliver both operational and financial gains without disrupting existing workflows.
FAQs About SCARA Robots
1. What is a SCARA robot best used for?
SCARA robots are ideal for high-speed, high-precision horizontal tasks like pick-and-place, small part assembly, screwdriving, packaging, and electronic component insertion. They perform best in repetitive operations that require tight tolerances and minimal vertical movement.
2. How many axes does a SCARA robot have?
Most SCARA robots have four axes:
- Base rotation (X-Y plane)
- Arm rotation (extension/retraction)
- Vertical Z-axis movement
- End effector rotation (θ-axis)
This structure allows fast planar movement with limited rotation.
3. Is a SCARA robot faster than a 6-axis robot?
Yes. SCARA robots are generally faster than 6-axis robots in short-range, horizontal operations due to their lighter structure and fewer joints. They can complete cycles in 0.3–0.5 seconds, making them suitable for high-throughput applications.
4. Can SCARA robots handle vision systems or dynamic part picking?
Absolutely. Many SCARA robots are compatible with machine vision systems and conveyor tracking, enabling them to detect part orientation, adjust on-the-fly, and perform precision placements even with moving parts.
5. What industries use SCARA robots the most?
SCARA robots are widely used in:
- Electronics (PCB and sensor assembly)
- Medical and pharmaceutical (device handling, packaging)
- Automotive (micro-assembly)
- Consumer goods (pick-and-place)
- Food and beverage (hygienic sorting and packing)
6. How accurate are SCARA robots?
Most industrial SCARA robots offer repeatability in the range of ±0.01 mm to ±0.02 mm, making them highly suitable for fine-detail tasks and micro-assembly.
7. Can SCARA robots be used in cleanroom environments?
Yes. Several SCARA models from brands like Stäubli, Epson, and Yamaha are rated for ISO Class 5 or better, making them ideal for cleanroom use in pharmaceuticals, medical device manufacturing, and semiconductor packaging.
Conclusion: Why SCARA Robots Are the Smart Choice for High-Speed Industrial Automation
In a manufacturing world driven by precision, speed, and efficiency, SCARA robots stand out as one of the most dependable solutions for repetitive, horizontal operations. Their selective compliance, compact design, high-speed capability, and cost-effectiveness make them the preferred choice for industries that need fast cycle times and consistent output—without compromising on quality.
From PCB assembly in electronics to sterile packaging in pharmaceuticals, SCARA robots have proven their value across sectors. As Industry 4.0 reshapes factory floors, SCARA systems are evolving with it—offering real-time data tracking, cloud connectivity, predictive maintenance, and seamless integration into smart production lines.
Whether you’re scaling up output, facing manpower challenges, or aiming to reduce operational defects, SCARA robots offer a future-ready path to intelligent automation.