Spot Welding Robots: The Ultimate Guide to Precision, Productivity, and Profit
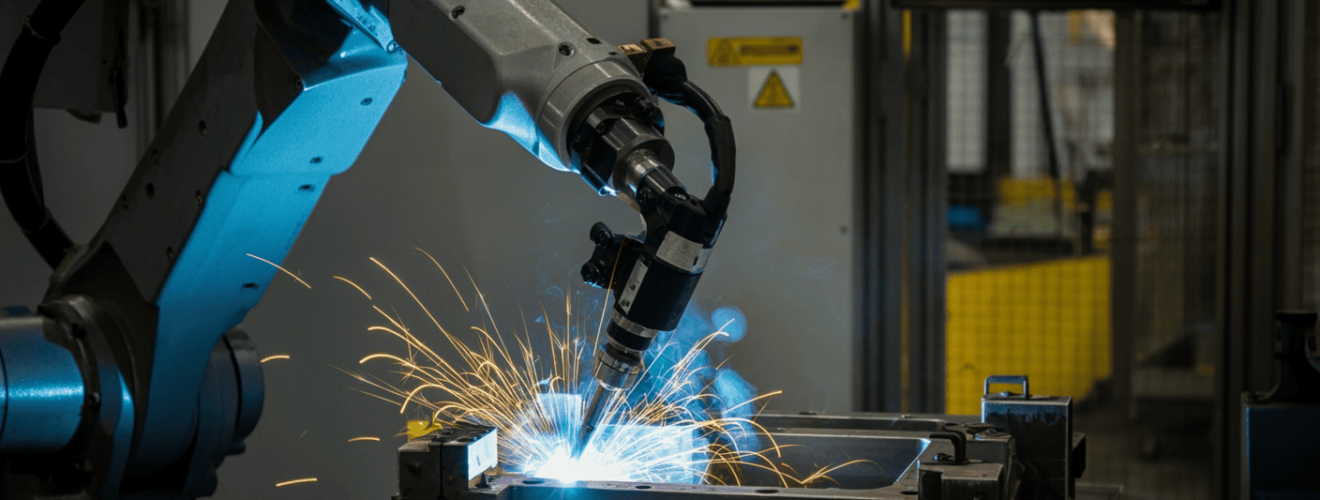
Four‑and‑a‑quarter million industrial robots now grind, weld, and assemble on factory floors worldwide—a record that keeps climbing every quarter. Yet many plants still battle labor shortages, inconsistent weld quality, and rising safety costs. Spot welding robots solve those headaches by delivering repeatable joints 24/7, often paying for themselves in under two years. In the next 20 minutes you’ll learn exactly how spot welding robots slash defects, speed up cycle time, and future‑proof your production line.
Table of Contents
What Exactly Is a Spot Welding Robot?
A Quick Definition
A spot welding robot is an articulated, usually six‑axis, industrial arm fitted with a resistance‑welding gun. It clamps two metal sheets between copper electrodes, sends a high current pulse through the stack, and forms a fused “nugget” in a fraction of a second.
Core Components
- Robot arm – supplies reach, payload, and repeatability.
- Weld gun – servo or pneumatic; applies force and current.
- Controller – coordinates motion, current, and force curves.
- Transformer & power supply – delivers the amperage burst.
- Fixture or jig – holds parts in a known position.
- Sensors – monitor force, electrode wear, or part presence.
Why Resistance Spot Welding?
- No filler metal needed.
- Cycle times measured in milliseconds.
- Minimal heat‑affected zone.
- Ideal for high‑volume sheet‑metal assemblies—especially auto bodies.
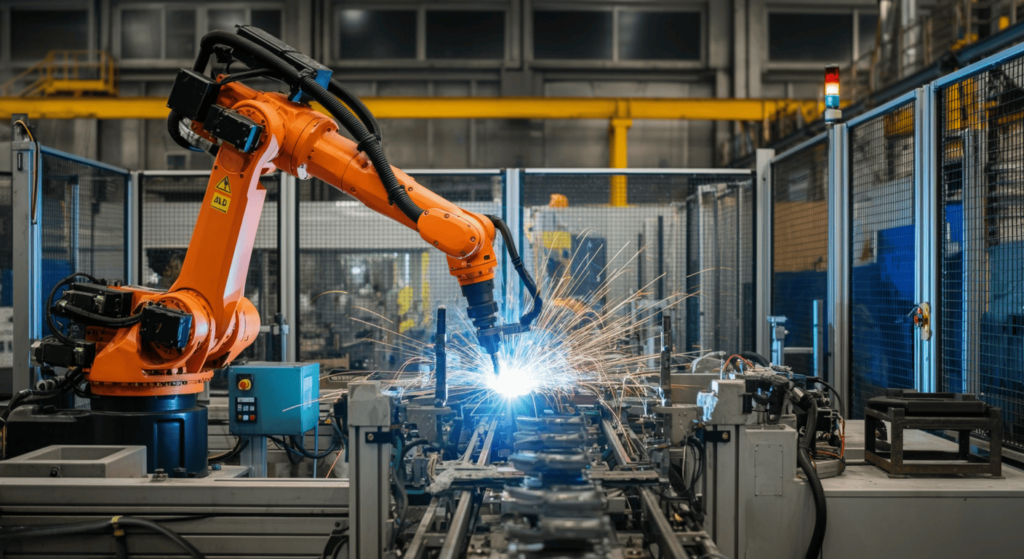
Why Manufacturers Are Racing to Deploy Spot Welding Robots
Consistent Weld Quality
Robots never tire, sneeze, or lose focus. Once programmed, they reproduce electrode force and current curves within tight tolerances, driving defect rates below 0.5 percent in world‑class lines.
Faster Cycle Times
Advanced path‑planning software can shave seconds off every weld sequence. A Brazilian body‑shop trimmed 6.6 percent from takt time by re‑balancing a 42‑robot line.
Lower Operating Cost
After the upfront capital, robots work three shifts for pennies per hour—no overtime, benefits, or sick days. Typical payback: 18‑24 months in automotive applications.
Safer Workplaces
OSHA lists electrical shock, fume inhalation, and eye injury among the top welding hazards. Robots remove operators from arc flash and pinch points, driving recordable incidents toward zero.
Solving the Labor Shortage
Welding is one of the hardest skilled trades to staff. Robots let companies redeploy scarce welders to higher‑skill inspection and programming roles.
Sustainability & Scrap Reduction
Tighter process control means fewer re‑works, less material waste, and lower energy per good part—metrics that now factor into ESG scorecards.
Key Industries and Applications
Industry | Typical Robot Duty | Why Robots Win |
---|---|---|
Automotive | Body‑in‑white panels, chassis rails | High volume, 4,000+ welds per vehicle |
Home Appliances | Washer & dryer cabinets | Cosmetic quality, thin‑gauge steel |
Aerospace | Seat tracks, brackets | Precise nugget size, traceability |
Construction Equipment | Cab frames | Thick material, ergonomic hazards |
Battery Packs | Module enclosures | Thermal management, tight tolerances |
How Spot Welding Robots Work—Step by Step
- Part Presentation – A conveyor or shuttle positions the assembly fixture.
- Robot Approaches – Path planning avoids clamps and neighboring robots.
- Electrode Force Applied – Servo gun squeezes sheets with 400–1,000 kgf.
- Current Pulse – Up to 30 kA flows for 100–600 ms, forming the nugget.
- Hold Time – Force is maintained while the nugget solidifies.
- Retract & Index – Robot moves to the next weld point; fixture may rotate.
Choosing the Right Spot Welding Robot
1. Payload & Reach
Ensure the arm can handle gun weight plus cables—often 100 kg or more.
2. Servo vs. Pneumatic Gun
Servo guns deliver closed‑loop force control and save compressed‑air costs.
3. Duty Cycle & IP Rating
High‑duty robots feature water‑cooled servos and IP67 wrists for harsh environments.
4. Controller Ecosystem
Look for offline‑programming compatibility (e.g., DELMIA, RobotStudio) and Industry 4.0 data hooks.
5. Collaborative vs. Traditional
Cobots with integrated force sensors suit low‑volume, high‑mix shops but sacrifice speed.
6. New, Refurbished, or Leasing
Refurb units cut cap‑ex by 40 percent, but verify remaining gun life and controller generation.
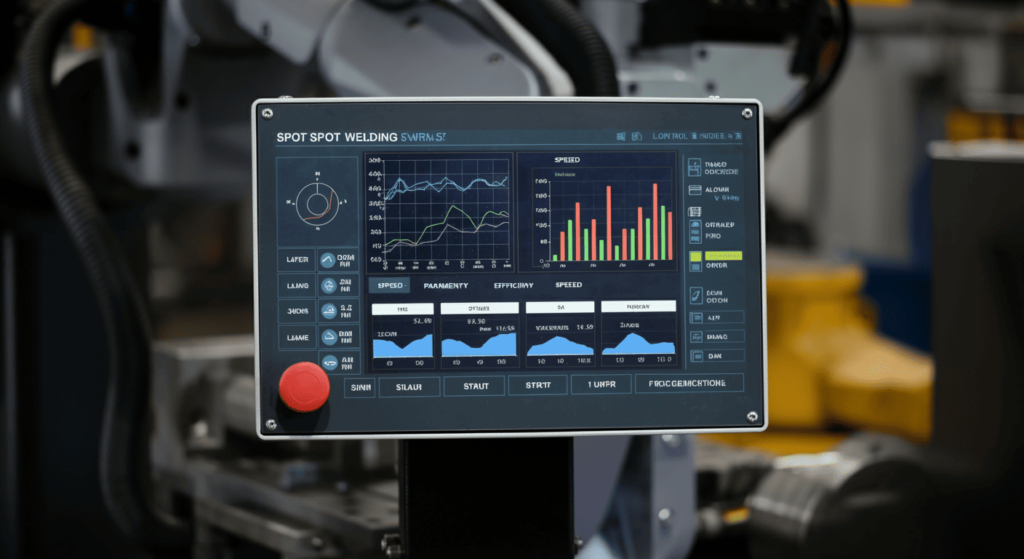
Implementation Roadmap
- Feasibility & ROI Study
- Collect part mix, weld count, takt time, and floor space.
- Simulation & Line Balancing
- Use digital twins to optimize torch angles and avoid singularities.
- Cell Design
- Layout fencing, light curtains, and maintenance zones per ISO 10218.
- Safety Compliance
- Meet OSHA 1910.255 low‑voltage control circuit rules.
- Training & Certification
- Enroll programmers in AWS’s Certified Robotic Arc Welding (CRAW) credential.
- Factory Acceptance Test (FAT)
- Verify cycle time, nugget size, and controller backups.
- Ramp‑Up & Continuous Improvement
- Track KPIs—overall equipment effectiveness (OEE), mean time to repair (MTTR), electrode life.
Common Challenges—and How to Beat Them
Challenge | Root Cause | Proven Fix |
---|---|---|
Expensive Electrode Wear | High current, dirty surfaces | Use dressers; schedule tip changes by weld count |
Misaligned Welds | Part tolerance stack‑up | Add proximity or vision sensors for seam tracking |
Excessive Spatter | Poor clamp force or current spikes | Tune force curve; clean electrodes; optimize schedules |
Robot Downtime | Cable dress, gun servo failure | Implement predictive maintenance with current sensors |
Line Bottlenecks | Unbalanced robot cycle times | Re‑sequence points; split tasks across dual arms |
Cost‑Benefit Analysis & Real‑World Case Studies
- A Midwestern metal‑stamping plant added three robotic cells and lifted profitability 12 percent in the first year by cutting scrap and rework.
- Re‑sequencing a 42‑robot body‑shop in Brazil reduced overall cycle time 6.6 percent without new hardware.
- A Kawasaki robot logged 38,390 hours—20 years of eight‑hour shifts—with only 57 maintenance events, proving long‑term durability.
Future Trends to Watch
- AI‑Driven Path Optimization – Ford already boosts assembly speed 15 percent by letting AI refine robot motions.
- Adaptive Welding Guns – Force and current auto‑adjust in real time via closed‑loop sensors.
- Digital Twins & Edge Analytics – Real‑time weld‑quality dashboards predict nugget failures before they happen.
- Lightweight Cobots – Safer to work beside humans, perfect for flexible body‑in‑white sub‑lines.
- Green Manufacturing Metrics – Expect ISO‑compliant energy dashboards on every new controller.
- Global Adoption Shift – China now outranks Germany in robot density, accelerating the competitive stakes.
Frequently Asked Questions (FAQ)
Q1. How much does a spot welding robot cost?
A fully integrated single‑robot cell ranges from $120,000 to $250,000, depending on gun type, fixturing, and safety hardware. Leasing and refurbished options can cut that in half.
Q2. Can one robot handle different models?
Yes. Modern controllers store multiple programs. Quick‑change tooling and barcode‑driven schedules let a robot switch jobs in under a minute.
Q3. What is the typical payback period?
Automotive lines often see payback in 18–24 months. Low‑volume job shops average 30–36 months due to smaller production runs.
Q4. How do robots improve weld quality?
Robots deliver precise electrode force, repeatable current pulses, and consistent positioning—eliminating the human variability that causes burn‑throughs and weak nuggets.
Q5. Do robots eliminate welding jobs?
They shift jobs rather than erase them. Demand for robot programmers, maintenance techs, and quality inspectors rises as manual welding declines.
Five Persistent Myths—Busted
- “Robots are only for big OEMs.”
Affordable cobots and leasing plans now put automation within reach of shops with fewer than 50 employees. - “Programming is rocket science.”
Drag‑and‑drop teach pendants and offline wizards cut programming time by 70 percent. - “Robots can’t handle thick material.”
Servo guns now deliver up to 1,000 kgf, making 3‑sheet joints in heavy equipment frames routine. - “Automation kills flexibility.”
Quick‑change tooling and digital twins let you swap models faster than re‑training a human crew. - “Quality audits become harder.”
Weld data is logged for every nugget, giving inspectors a digital trail manual welding can’t match.
Conclusion
Spot welding robots are no longer futuristic luxuries; they’re table‑stakes for manufacturers that want higher throughput, consistent quality, and safer working conditions. By selecting the right robot, planning a phased rollout, and embracing data‑driven optimization, you can achieve double‑digit gains in OEE while cutting costs and emissions. If you’re ready to see how spot welding robots fit into your plant, start with a feasibility study—and let the numbers speak for themselves. Share your questions below or subscribe for more deep‑dive automation guides.
Further Reading & Source Links
- International Federation of Robotics – World Robotics 2024 Report. ifr
- International Federation of Robotics – World Robotics 2023 Report. ifr
- OSHA Standard 1910.255 – Resistance Welding. osha
- OSHA Welding, Cutting & Brazing Overview. osha
- American Welding Society – Why Fabricators Choose Automated Welding. aws
- AWS Welding Journal – Collaborative Robot Welding Packages. aws
- AIChE Journal – Cycle‑Time Optimization for Robotic Spot Welding. aiche.onlinelibrary.wiley
- ResearchGate – Balancing a Robotic Spot Welding Line: Industrial Case Study. researchgate
- ICR Services – Spot Welding Robotic Cell Case Study. icrservices
- Kawasaki Robotics – Reliable Robot Welds for 20 Years. kawasakirobotics
- NIST – Industrial Robot Technology and Productivity Improvement. tsapps.nist
- NIST – Measurement Science for Manufacturing Robotics (2024). tsapps.nist
- AZoRobotics – Robots in Automotive Welding. azorobotics
- Force Design – Robots for Resistance Welding in Automotive Applications. forcedesign
- Reuters – China Overtakes Germany in Industrial Robot Density. reuters
- Wired – Ford’s AI‑Enhanced Robots Speed Assembly Lines. wired