Delta Robots (Parallel Robots): The High-Speed Future of Precision Automation
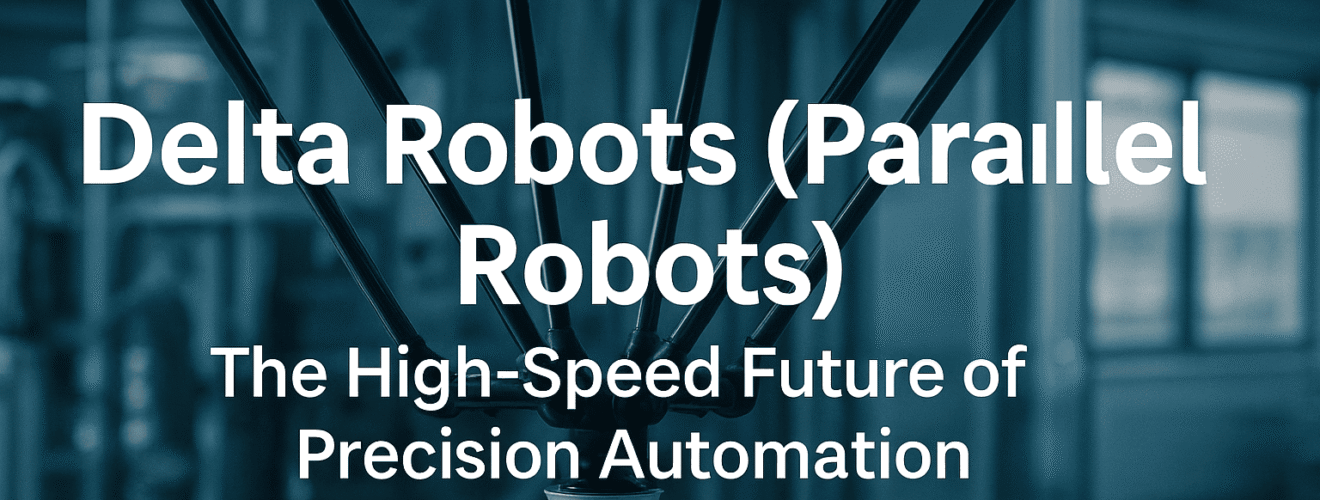
Imagine a robot that can sort 300 chocolate bars per minute—without breaking a sweat or misplacing a single one.
In today’s fast-paced manufacturing world, precision isn’t enough. Speed is king. Industries like food packaging, pharmaceuticals, and electronics demand automation that doesn’t just work—but works fast, works flawlessly, and works without pause. That’s where Delta Robots, also known as Parallel Robots, come in.
Engineered for high-speed pick-and-place tasks, Delta robots are compact, ceiling-mounted marvels capable of blistering acceleration and pinpoint accuracy. They’ve transformed everything from tray filling and sorting to lightweight assembly and micro-picking on conveyor belts.
In this comprehensive guide, you’ll learn:
- What Delta (parallel) robots are and how they work
- Where they outperform traditional robots
- How they’re being used in real-world factories today
- What to consider when choosing the right Delta robot for your plant
Whether you’re an automation engineer, OEM integrator, or plant manager exploring next-gen solutions, this guide will help you decide if Delta robots are the right fit for your operation.
Table of Contents
What Are Delta Robots (Parallel Robots)?
Delta robots, also known as parallel robots, are high-speed robotic arms designed for lightweight, precision operations like sorting, packing, and assembling. They feature a unique structure that distinguishes them from conventional serial robots such as SCARA or 6-axis articulated arms.
Unlike those designs, where each joint is stacked on the previous one, Delta robots use a parallel configuration of arms—usually three or four—that connect a fixed base to a mobile platform. These arms work together to move an end effector (such as a gripper or suction cup) quickly and smoothly in the X, Y, and Z axes, with some models also offering limited rotation (Theta).
This design gives Delta robots:
- Blazing speed
- High repeatability
- Low inertia due to lightweight moving parts
Key Fact: Delta robots were invented in the 1980s by Reymond Clavel at the École Polytechnique Fédérale de Lausanne (EPFL), originally to automate tasks like chocolate sorting. Since then, they’ve evolved into one of the fastest robotic platforms used in modern industry.
Typical Features:
- 3 Translational Degrees of Freedom (X, Y, Z)
- 1 Optional Rotational Axis (θ)
- Ceiling-mounted or gantry-mounted structure
- End effector fixed beneath a dome-shaped work envelope
- Ideal payload range: 1–5 kg (though some heavy-duty variants exist)
Real-World Analogy:
Think of a Delta robot like a spider hanging from a web—moving its body rapidly and precisely to catch tiny insects flying beneath it. Now replace the spider with a robotic gripper and the insects with packaged food, microchips, or vials—that’s essentially how a Delta robot works on your factory floor.
How Delta Robots Work: Parallel Kinematics Explained
To truly appreciate the speed and agility of a Delta robot, you need to understand what sets its motion system apart from traditional robots.
Unlike serial robots—where each joint sits on top of the last (like a human arm)—Delta robots use a parallel kinematic architecture. This design distributes motion across multiple linkages, all working together to control a single moving platform suspended beneath a fixed base.
Core Structure of a Delta Robot
A typical Delta robot includes:
- Fixed Triangular Base:
Mounted to a frame, ceiling, or gantry, this remains stationary while housing the motors and drives. - Three (or Four) Parallel Arms:
Each arm consists of an upper actuator arm (motor-driven) and a passive parallelogram linkage. These arms guide the motion of the moving platform below. - Mobile Platform (End Effector Mount):
The joint location where all arms converge. This is where the gripper, suction cup, or tool is mounted. - (Optional) Rotational Axis (Theta):
A fourth motor or passive joint can provide limited rotation, enabling orientation of parts during placement.
How the Motion Works
Each motor in the fixed base controls one upper arm. These arms move independently but in synchronized trajectories. When the motors rotate:
- The arms shift the position of the mobile platform in real-time.
- The three actuators together define precise XYZ coordinates.
- Movement is achieved through parallel motion, reducing load and increasing responsiveness.
Because the motors are not on the moving parts, inertia is extremely low, allowing for rapid accelerations and decelerations—a key reason Delta robots are the fastest pick-and-place systems in the world.
Advantages of Parallel Kinematics Over Serial Kinematics
Feature | Delta Robot (Parallel) | SCARA/6-Axis (Serial) |
---|---|---|
Speed | Extremely high | Medium to high |
Payload on moving arm | Very low (motors stay fixed) | High (motors add weight) |
Stiffness | High | Moderate |
Control complexity | High | Lower |
Workspace shape | Dome-shaped | Cylindrical or spherical |
🧠 Real-World Analogy
Think of three puppeteers holding strings tied to a puppet from above. Each pulls or relaxes their string to move the puppet in a different direction. When coordinated perfectly, they can make the puppet fly, dip, or spin with astonishing precision and speed.
That’s essentially how a Delta robot’s motors control its end effector—tightly synchronized movements from fixed arms guiding a floating platform with surgical precision.
Motion Characteristics
- Range of Motion: Dome-shaped or semi-spherical working area
- Degrees of Freedom: 3 translational (X, Y, Z), 1 optional rotational
- Cycle Times: As low as 0.3 seconds per pick-and-place operation
- Repeatability: Typically ±0.1 mm, depending on the model and application
Key Advantages of Delta Robots
Delta robots are specifically engineered to do one thing better than almost any other robot: move small parts quickly and accurately in three-dimensional space. Their design delivers a host of performance advantages that make them the preferred choice in ultra-fast, high-precision environments.
Let’s break down the core benefits of Delta robots.
1. Blazing-Fast Speeds
Delta robots are built for speed—period.
Their lightweight arms and parallel structure allow them to:
- Complete 200–300 picks per minute
- Accelerate and decelerate rapidly without overshoot
- Maintain precision even at high throughput
Real-world example: In food packaging lines, Delta robots routinely pick and place candy, bakery items, or small sachets faster than any human—or most other robots—can manage.
2. Minimal Moving Mass = Low Inertia
Because all motors are mounted at the base (not on the arms), the only moving parts are the lightweight linkages and the tool mount.
Benefits:
- Lower wear and tear
- Less energy required per movement
- Quieter operation
- Longer service life with fewer mechanical failures
This also enables Delta robots to work longer hours at peak performance—perfect for 24/7 production cycles.
3. High Accuracy and Repeatability
Delta robots offer repeatability levels of ±0.1 mm, depending on configuration.
This makes them ideal for:
- Precision assembly
- Tray filling with exact spacing
- Vision-guided tasks where part position varies slightly
Insight: Delta robots combine speed with consistency—critical for high-volume applications that require near-zero tolerance for errors.
4. Overhead Mounting = More Floor Space
Delta robots are typically mounted above the working area. This offers several layout advantages:
- Uncluttered workspace
- Easier conveyor integration
- Safer environments (no ground-level moving parts)
- Flexible use of space under the robot for trays, bins, or conveyors
This is particularly helpful in cleanroom or high-density automation cells.
5. Ideal for Conveyor Tracking and Vision Integration
Delta robots are often paired with:
- Vision systems to locate randomly oriented parts
- Conveyor tracking to grab moving products on-the-fly
This makes them extremely useful in:
- Food sorting
- Electronics packaging
- Pharmaceutical batch processing
Their quick reaction time and ability to follow dynamic input make Delta robots the top choice for flow-based production lines.
6. Cleanroom and IP-Rated Versions Available
Many Delta robots are designed for:
- Cleanroom operations (ISO 5 and ISO 6)
- Washdown environments (IP65 or higher)
This makes them ideal for:
- Medical device assembly
- Sterile pharma packaging
- Food-grade processing lines
Quick Comparison: Why Delta Robots Excel
Advantage | Why It Matters |
---|---|
Ultra-fast cycle time | Higher throughput with fewer robots |
Minimal moving weight | Less wear, more uptime |
Ceiling-mounted | Saves space and improves accessibility |
Precision placement | Reduces rework and rejects |
Easy vision integration | Works in dynamic or mixed-part environments |
Delta robots are not generalists—they’re specialists. If your application involves high-speed, high-precision, low-payload tasks, a Delta robot is almost always the best choice.
Common Applications of Delta Robots in Industry
Delta robots are built for speed, precision, and consistency—which makes them ideal for industries where repetitive motion, fast cycle times, and compact layouts are critical. Below are the most common sectors where Delta robots thrive and the tasks they handle best.
1. Food and Beverage Industry
Use Cases:
- Sorting chocolates, cookies, pastries, and snack bars
- Placing bakery items into plastic trays
- Picking items from conveyor belts for secondary packaging
- Handling fragile or shape-sensitive items (e.g., croissants or fruits)
Why Delta Works:
Cleanroom-compatible models, fast cycle time, non-contact gripping options (e.g., vacuum), and stainless-steel or IP-rated bodies make Delta robots a go-to solution in food processing lines.
Example: A biscuit manufacturer uses Delta robots to load 240 biscuits per minute into trays, reducing labor dependency by 75% and increasing hygiene standards.
2. Pharmaceutical and Medical Device Assembly
Use Cases:
- Vial and syringe sorting
- Transferring blister packs or capsules
- Picking medical device components for assembly
- Loading/unloading sterile packaging cells
Why Delta Works:
Delta robots offer precise, hygienic, contactless motion in environments where contamination is a risk. ISO 5/6 cleanroom-rated models are often standard in pharmaceutical plants.
Example: A pharmaceutical packaging unit deployed three Delta robots to sort and insert pre-filled syringes into sterilized containers—achieving 98.9% accuracy and cutting rework in half.
3. Electronics Manufacturing
🔌 Use Cases:
- Component placement onto PCBs
- LED and chip handling
- Tray-based sorting of connectors, resistors, capacitors
- Light assembly tasks (with vision-assisted orientation)
Why Delta Works:
Delta robots combine delicate touch with high speed. They can work closely with machine vision systems to ensure perfect orientation of tiny, high-value components.
Example: An LED manufacturing unit used Delta robots with vision tracking to align and sort LEDs at 280 picks per minute—reducing manual misplacements by 90%.
4. Consumer Goods and Personal Care
Use Cases:
- Sorting cosmetic items (lipsticks, bottles, tubes)
- Tray loading for secondary packaging
- Handling small toys, fasteners, caps, etc.
Why Delta Works:
Delta robots handle a wide variety of SKUs in limited spaces and can switch between product types with minimal changeover time.
Example: A personal care product company deployed Delta robots for handling tube inserts into boxes with random orientation—achieving full ROI in just 14 months.
5. Logistics and E-Commerce Fulfillment
Use Cases:
- Sorting parcels or pouches into bins
- Automated order picking (low-weight SKUs)
- Pick-and-drop between conveyor lanes
- Loading packages into cartons
Why Delta Works:
With vision and barcode integration, Delta robots can dynamically sort and pack products at lightning speed in fulfillment centers or micro-warehouses.
Example: An e-commerce startup reduced its manual SKU sorting time by 60% after installing Delta robots to handle 100+ item types per shift.
6. 3D Printing (Delta Configuration)
Use Cases:
- Delta-structured 3D printers for fast vertical builds
- High-speed polymer prototyping
- Smooth curved layer printing
Why Delta Works:
In vertical 3D printing setups, delta kinematics allows smoother circular paths and quicker Z-axis adjustments—especially in open-source and experimental printing labs.
Summary Table: Delta Robot Applications by Industry
Industry | Common Tasks | Key Benefit |
---|---|---|
Food & Beverage | Sorting, packaging, tray loading | Hygiene + speed |
Pharma & Medical | Vial/blister handling, sterile packaging | Precision + cleanroom readiness |
Electronics | Component placement, chip handling | Micron accuracy + vision integration |
Consumer Goods | Cosmetic handling, light assembly | SKU flexibility + high output |
Logistics/E-Com | Bin picking, sorting | Speed + barcode integration |
3D Printing | Prototyping, layer shaping | Smooth motion + rapid prototyping |
Delta Robots vs Other Industrial Robots
Delta robots aren’t one-size-fits-all. Their speed and precision make them ideal for certain applications—but not every one. Depending on your production needs, payloads, and motion requirements, other robots like SCARA, Cartesian, or 6-axis arms may be better suited.
Let’s compare them across key dimensions.
Delta Robot vs SCARA Robot
Feature | Delta Robot | SCARA Robot |
---|---|---|
Speed | Extremely high (up to 300 ppm) | Very high (150–200 ppm) |
Payload | Light (1–5 kg) | Light to medium (up to 20 kg) |
Mounting | Overhead | Table or floor-mounted |
Workspace shape | Dome-like | Cylindrical |
Best For | High-speed sorting, tray filling | Assembly, screwdriving, insertion |
Vision Integration | Excellent | Excellent |
Flexibility (rotation) | Limited | Moderate |
Verdict: Use Delta robots for ultra-fast picking. Choose SCARA for horizontal assembly or insertions with moderate complexity.
Delta Robot vs Cartesian Robot
Feature | Delta Robot | Cartesian Robot |
---|---|---|
Motion Type | Parallel kinematics | Linear axes (X, Y, Z) |
Speed | Very high | Medium |
Flexibility | Low (limited reach & rotation) | High (customizable size & stroke) |
Payload | Light | Heavy (20 kg–100 kg+) |
Space Required | Small (overhead mount) | Large (frame needed) |
Best For | Small part sorting | Palletizing, heavy item movement |
Verdict: Delta is better for small, high-speed items. Cartesian is better for large payloads, long strokes, or custom gantry systems.
Delta Robot vs 6-Axis Robot (Articulated)
Feature | Delta Robot | 6-Axis Robot |
---|---|---|
Axes of movement | 3–4 | Full 6 (X, Y, Z, pitch, yaw, roll) |
Motion flexibility | Low | Very high |
Speed | Very high | Moderate |
Programming complexity | Moderate | High |
Payload capacity | Light | Medium to heavy (up to 200 kg) |
Best For | Sorting, packaging | Welding, painting, 3D contour tasks |
Verdict: Use Delta for speed. Use 6-axis when you need articulated motion in all directions or working around obstacles.
Quick Selection Guide: Which Robot to Use?
Task | Best Robot Type |
---|---|
Pick-and-place @ 250+ cycles/min | Delta |
Horizontal insertion (PCBs, plugs) | SCARA |
Box palletizing or large loads | Cartesian |
Complex tool paths (welding) | 6-Axis Articulated |
Delta robots outperform all other types when:
- Your task is repetitive, high-speed, and lightweight
- Floor space is limited
- Conveyor and vision system integration is required
- Cleanroom or washdown environments demand minimal mechanical exposure
Limitations of Delta Robots
Delta robots are incredibly fast and precise, but they’re not designed for every automation scenario. Like any specialized tool, they have performance boundaries that should be understood before selecting them for an application.
Here are the key limitations to consider:
1. Limited Payload Capacity
Delta robots are optimized for speed—not strength. Their structure allows for lightning-fast motion only with lightweight payloads, typically ranging between 1–5 kg.
Limitation:
If your application involves moving heavy components, metal parts, or multi-part assemblies, a Cartesian or 6-axis robot is a better choice.
2. Restricted Range of Motion
Delta robots provide 3 translational degrees of freedom (X, Y, Z), with an optional fourth for limited rotation (θ). They cannot:
- Tilt objects
- Reach around obstacles
- Perform complex orientation tasks (like welding, polishing, or curved path movement)
Limitation:
If your task requires 3D orientation, pitching, or rolling, a 6-axis robot is essential.
3. Small Working Volume
Delta robots typically operate in a dome-shaped or semi-spherical working envelope. This compact area is ideal for tray or conveyor-based layouts, but:
Limitation:
They are not suitable for long-range horizontal or vertical motion, like in palletizing or large-box sorting.
4. Complexity in Setup and Calibration
Delta robots use parallel kinematics, which require:
- Precision during initial installation
- Calibration of arm lengths and angular limits
- Complex inverse kinematic algorithms for motion planning
Limitation:
This can result in a longer commissioning time and more specialized programming expertise than simpler Cartesian or SCARA setups.
5. High-Speed Safety Requirements
Because Delta robots move incredibly fast, any human interaction during operation must be carefully managed.
📌 Limitation:
They often require:
- Full enclosures or safety cages
- Light curtains or vision-based safety systems
- Emergency stop integrations
This increases the cost and complexity of safety compliance in manual/robot hybrid zones.
Summary Table: Limitations of Delta Robots
Limitation | Description | Better Alternative |
---|---|---|
Low payload capacity | Typically <5 kg | Cartesian or 6-axis |
Limited rotational flexibility | No tilt, pitch, or roll | 6-axis articulated arm |
Small workspace | Confined dome area | Cartesian/gantry robots |
Complex calibration/setup | Requires advanced programming and tuning | SCARA or Cartesian |
Speed-related safety measures | Needs advanced safety enclosures and protocols | SCARA/low-speed arms |
Understanding these limitations ensures you’re not just buying automation—you’re investing in the right automation for your task.
How to Choose the Right Delta Robot
Not all Delta robots are created equal. While they share the same basic design, their performance varies greatly based on payload capacity, working envelope, motion speed, and integration capability.
Before making a purchase or integrating one into your line, consider these critical selection factors:
1. Define Your Payload Requirements
The payload includes:
- The product being handled
- The end effector (gripper, suction cup, etc.)
- Any connectors, tool changers, or sensors
Tip: Choose a robot with at least 20–30% extra payload capacity than your maximum expected load. This ensures stability, reduces strain, and allows future scalability.
2. Determine Your Speed and Cycle Time Goals
If your production line needs to move:
- 100+ products per minute
- With pick-and-place cycles under 0.5 seconds
Then choose a Delta robot rated for high-speed motion with minimal settling time.
Considerations:
- Typical speeds: 60–300 picks/min
- Balance speed with repeatability (don’t sacrifice accuracy for raw motion)
3. Understand Your Workspace and Mounting Constraints
Delta robots work best when mounted overhead:
- Gantry-style or ceiling brackets
- Above conveyors, trays, or rotating tables
Ask:
- Is the robot’s working envelope (dome or cone-shaped) large enough to reach all pick and place zones?
- Will the base interfere with cameras, light curtains, or feeders?
Common working diameters: 300 mm to 1600 mm
4. Evaluate Repeatability and Precision Needs
For electronics, medical, or packaging:
- Look for repeatability of ±0.1 mm or better
- Ensure stable control of XYZ motion and end-effector alignment
Application Fit:
Precision adhesive application or micro-assembly requires tighter tolerances than tray loading or sorting.
5. Choose the Right End Effector
Delta robots are compatible with:
- Vacuum suction cups (ideal for flat items)
- Two- or three-finger grippers
- Magnetic pickers
- Custom-designed EOATs
Tip: Ensure the robot has:
- Sufficient I/O ports
- Tool Center Point (TCP) calibration features
- Compatible flange for mounting your tool
6. Check Compatibility with Vision and Conveyor Systems
Many Delta robots are used in:
- Random part orientation setups (with vision)
- Dynamic conveyor tracking environments
Ask:
- Does the model support camera integration (GigE, USB3, etc.)?
- Can it track moving parts and compensate in real time?
7. Assess Environmental Requirements
Depending on your industry, the robot may need to be:
- IP65 or IP69K-rated for water resistance
- ISO Class 5 or 6 cleanroom certified
- Built from stainless steel or other hygienic materials
Industries Affected:
Food, pharmaceuticals, medical devices, cosmetics
8. Review Software and Programming Interface
Good programming = faster deployment.
Look for:
- Graphical user interfaces
- Drag-and-drop teaching
- Camera calibration tools
- Support for industrial protocols (Ethernet/IP, PROFINET, etc.)
Some vendors even offer simulation tools to test robot logic before on-site installation.
9. Check Vendor Reputation and Support
Before selecting a Delta robot, ask vendors:
- Can they provide local installation and training?
- Do they offer remote diagnostics and service?
- What is the lead time for spare parts?
- Do they have references in your industry?
Tip: Always request a demo or case study before committing.
Recommended Global Delta Robot Brands
Brand | Known Models | Strengths |
---|---|---|
ABB | FlexPicker IRB 360 | Hygiene, food, high-speed lines |
FANUC | M-1iA, M-2iA | Compact, fast, vision ready |
Omron | Quattro and Hornet Series | Multi-axis, EtherCAT compatible |
Codian | D4, D5, D6 Series | Stainless steel, pharma packaging |
Stäubli | TP80 Fast Picker | Cleanroom, ISO Class 5 certified |
Case Study: Delta Robot Deployment in a Food Packaging Line
Client Overview
- Industry: Food Processing & Packaging
- Product: Packaged cookies and snack bars
- Location: Gujarat, India
- Challenge: Manual tray loading was inconsistent, slow, and caused frequent line stoppages due to human fatigue and misalignment errors.
The Problem
Before automation, the client relied on:
- Four operators manually sorting and placing snacks into trays
- Line output capped at ~120 trays per minute
- Frequent delays due to human error and rest periods
- Product damage from rough handling
- Inability to scale production during seasonal demand
Objective:
Implement a robotic solution that could:
- Handle products with variable orientation
- Match or exceed manual speed
- Fit into existing space constraints without reconfiguring conveyors
- Maintain food hygiene standards (washdown-compatible)
The Solution: Delta Robot Integration
Robotic Cell Specs:
- Robot Type: Stainless-steel Delta robot with IP69K rating
- Speed: Configured for 240 pick-and-place cycles per minute
- Vision: Dual-camera setup for orientation correction
- End Effector: Multi-cup vacuum gripper for gentle handling
- Mounting: Gantry frame over existing conveyor line
- Control: Integrated with existing PLC and SCADA
- Safety: Light curtains, HMI alerts, and emergency stop
Installation Timeline
- Design & Simulation: 2 weeks
- Fabrication & FAT: 3 weeks
- On-site Installation: 4 working days
- Operator Training: 2 days
- Full Go-Live: Within 5 weeks of project start
Results After 3 Months
Metric | Pre-Automation | Post Delta Robot Deployment |
---|---|---|
Trays filled per minute | ~120 | 240+ |
Human operators per shift | 4 | 1 (monitoring only) |
Product misplacement rate | 2.6% | <0.4% |
Line downtime due to error | 9 hours/month | 1.5 hours/month |
ROI Payback Period | — | ~15 months |
Hygiene audit compliance | Manual logs | Automated data tracking |
Key Benefits Experienced
- Doubled production output without adding manpower
- Improved product presentation and packaging consistency
- Enhanced worker safety by reducing manual strain
- Streamlined quality reporting for food safety audits
- Scalable system ready to handle new SKUs in the future
This case illustrates how Delta robots—when correctly selected and integrated—can revolutionize productivity, consistency, and compliance in even modest-sized facilities
Delta Robots in Industry 4.0 and Smart Manufacturing
Delta robots aren’t just fast—they’re smart, connected assets in the modern factory. As Industry 4.0 reshapes production with automation, data, and artificial intelligence, Delta robots have evolved to meet the demands of this new era.
Let’s explore how they contribute to the digital transformation of manufacturing.
1. IoT Connectivity and Real-Time Data Monitoring
Modern Delta robots come equipped with:
- IoT-ready controllers
- Ethernet/IP, PROFINET, EtherCAT support
- Direct integration into SCADA, MES, and ERP systems
What It Enables:
- Live monitoring of pick rate, fault counts, idle time, and energy consumption
- Cloud dashboards for remote access and factory-wide visibility
- Instant alerts for temperature rise, motor load, or mispicks
Result: Improved responsiveness, faster decision-making, and real-time KPIs like OEE (Overall Equipment Effectiveness).
2. Predictive Maintenance Through Sensor Data
Delta robots can be embedded with smart sensors that track:
- Joint wear
- Motor vibration
- Arm acceleration/deceleration patterns
- Pick cycle drift
This data is analyzed to predict failures before they happen.
Result:
Reduced unplanned downtime, better spare part planning, and longer machine lifespan—all key components of lean manufacturing.
3. Seamless MES and ERP Integration
Delta robots can feed critical operational data into:
- Manufacturing Execution Systems (MES) for batch tracking
- Enterprise Resource Planning (ERP) tools for supply chain forecasting
Use Case: A food plant uses Delta robot data to automatically adjust raw material planning based on actual output vs. planned throughput.
4. Machine Vision + AI Integration
In Industry 4.0 setups, Delta robots are often combined with:
- Vision systems for random part orientation and defect detection
- AI-based software for adaptive picking, self-correction, or SKU changeovers
- Barcode and QR code scanners for traceability
Benefit: Increased automation flexibility and hands-free quality control.
5. Role in Dark Factories and Lights-Out Operations
Because Delta robots require minimal human intervention once programmed, they’re ideal for:
- Unmanned night shifts
- Automated packaging cells
- Fully robotic micro-fulfillment centers
With the right support systems (AMRs, conveyors, sorters), Delta robots can run 24/7 in lights-out manufacturing environments—reducing labor cost while increasing output.
Summary: Delta Robots and Smart Manufacturing
Industry 4.0 Feature | Delta Robot Role |
---|---|
IoT/Edge Connectivity | Live data on motion, speed, energy, and health |
Predictive Maintenance | Detects failures before they occur |
Vision + AI Automation | Adaptive sorting and real-time decision-making |
Cloud Dashboards | Factory-wide performance visibility |
Smart Production Planning | Real-time integration with MES and ERP |
Delta robots are no longer just motion machines—they’re data-driven performers powering the most modern production lines.
FAQs About Delta Robots (Parallel Robots)
1. What is a Delta Robot used for?
Delta robots are primarily used for high-speed pick-and-place, sorting, packaging, and light assembly tasks. They are ideal for applications in food processing, pharmaceuticals, electronics, and logistics where speed and precision are critical.
2. What is the working principle of a Delta Robot?
A Delta robot operates using three or more arms connected in parallel between a fixed base and a mobile platform. By controlling the angles of the upper arms, the robot moves the end effector precisely in 3D space—usually for fast, repetitive tasks with light payloads.
3. How fast can a Delta Robot operate?
Industrial Delta robots can perform up to 300 pick-and-place operations per minute, depending on payload, path distance, and application. This makes them one of the fastest robot types available for automation.
4. What is the maximum payload capacity of a Delta Robot?
Most Delta robots are designed for payloads between 1 kg and 5 kg. Some specialized models may handle up to 10 kg, but speed and precision may decrease as payload increases.
5. Can Delta Robots be used in cleanrooms?
Yes. Many Delta robots are cleanroom certified (ISO Class 5 or 6) and come with IP65/IP69K-rated bodies. This makes them suitable for sterile environments in pharmaceuticals, medical devices, and food-grade packaging.
6. What is the difference between a Delta robot and a SCARA robot?
Delta robots use parallel kinematics and are mounted overhead for ultra-fast sorting and picking. SCARA robots use serial kinematics and are better for horizontal assembly tasks that involve precise insertions or medium payloads.
7. Are Delta robots easy to program?
Most modern Delta robots are equipped with user-friendly interfaces, graphical programming environments, and vision system support. However, initial calibration and motion logic can be complex due to inverse kinematics.
Conclusion: Why Delta Robots Are a Game-Changer for High-Speed Precision Automation
In industries where every second matters—whether it’s packaging food, sorting medical vials, or assembling micro-electronics—Delta robots deliver unmatched speed, repeatability, and reliability.
Their lightweight, parallel-arm design allows for lightning-fast pick-and-place cycles, overhead mounting saves valuable floor space, and cleanroom compatibility makes them ideal for sensitive environments. When paired with vision systems and smart factory tools, Delta robots evolve from simple sorters into intelligent, IoT-connected assets that drive efficiency, accuracy, and growth.
Whether you manage an FMCG packaging line or an advanced electronics cell, the question isn’t “Do you need a Delta robot?”—it’s “How much productivity are you losing without one?”
Ready to Automate with Delta Robots? Let’s Talk.
At EngiTech, we help businesses:
- Evaluate and select the right Delta robot based on task, layout, and speed
- Integrate with conveyors, cameras, and SCADA systems
- Ensure hygiene, safety, and compliance with FSSAI, FDA, or ISO standards
- Achieve faster ROI with ongoing technical support and performance tuning
Need a feasibility study or demo?
Let’s automate your packaging, sorting, or assembly zone with precision and confidence.