Inspection Robots: The Ultimate Guide to Automated Inspection Technology in 2025
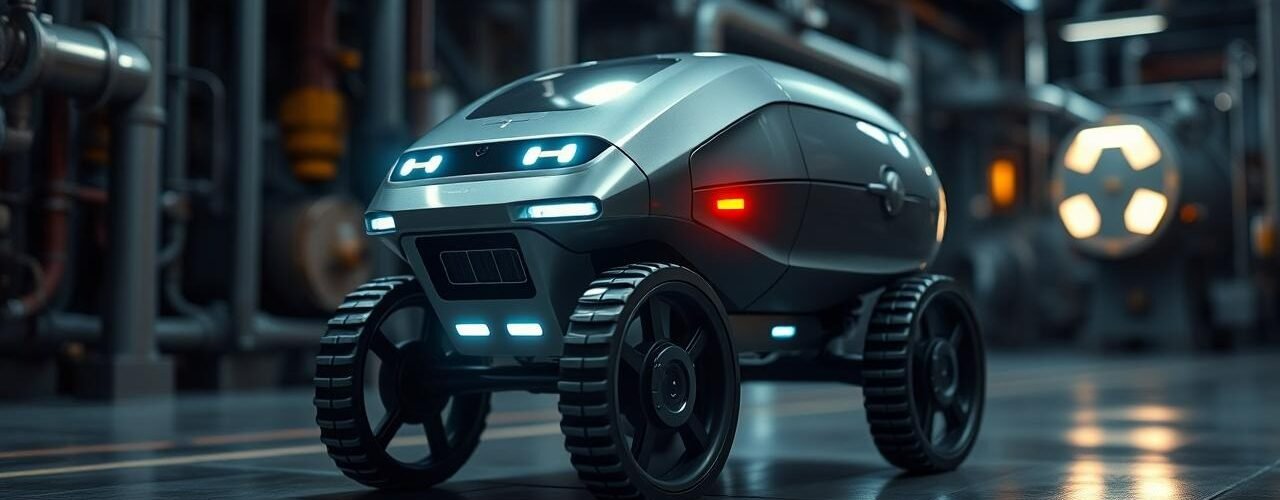
Do you know that inspection robots can reduce workplace accidents by up to 70% while improving inspection accuracy by 45%? In industries where human inspectors face hazardous conditions, these automated marvels are revolutionizing how companies maintain infrastructure, ensure quality control, and protect worker safety. Whether you’re managing industrial facilities, overseeing critical infrastructure, or simply fascinated by the latest robotics innovations, inspection robots represent one of the most significant technological advancements of the past decade.
This comprehensive guide will explore everything you need to know about inspection robots—from their fundamental capabilities and various types to the incredible benefits they offer across different industries. We’ll also examine the challenges they present, how to implement them in your operations, and what the future holds for this rapidly evolving technology.
Table of Contents
What Are Inspection Robots?
Inspection robots are specialized autonomous or semi-autonomous machines designed to examine, assess, and monitor environments, structures, or components that may be difficult, dangerous, or inefficient for humans to inspect. Using advanced sensors, cameras, and artificial intelligence, these robots can detect defects, anomalies, and potential issues with remarkable precision and consistency.
Core Capabilities of Modern Inspection Robots
Modern inspection robots come equipped with an impressive array of capabilities that allow them to perform complex inspection tasks:
- Visual Inspection: High-definition cameras and computer vision systems enable robots to detect surface flaws, structural issues, and visual anomalies.
- Non-Destructive Testing (NDT): Many inspection robots incorporate ultrasonic, radiographic, or thermal imaging technologies to assess internal structures without causing damage.
- Environmental Monitoring: Sensors detect temperature variations, gas leaks, radiation levels, and other environmental factors that might indicate problems.
- Data Collection and Analysis: AI-powered systems collect, process, and analyze inspection data in real-time, often identifying patterns and potential issues that human inspectors might miss.
- Remote Operation: Many inspection robots can be controlled from a safe distance, allowing operators to direct inspections in hazardous environments.
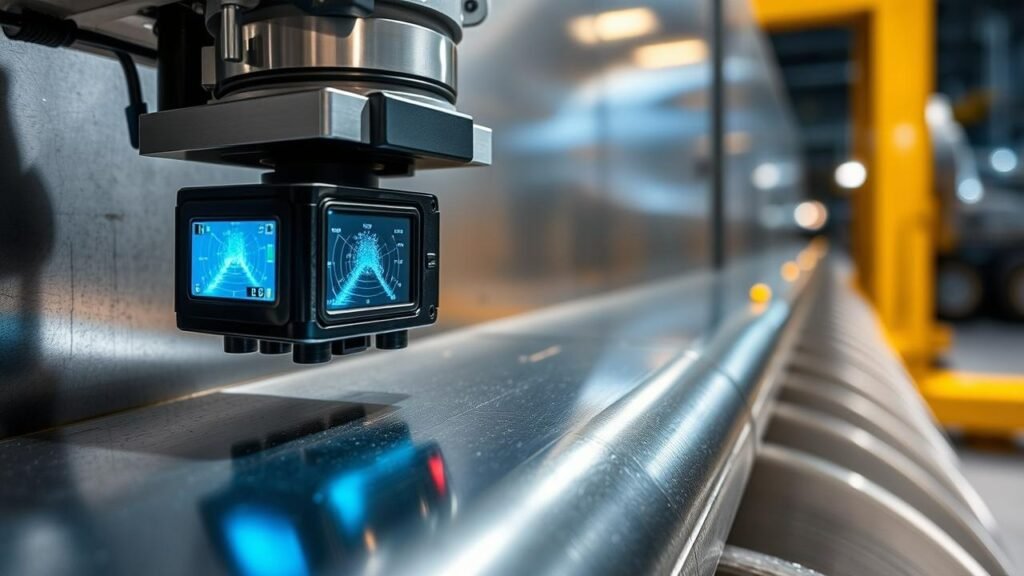
Why Inspection Robots Matter Now More Than Ever
The adoption of inspection robots has accelerated dramatically in recent years, driven by several key factors:
- Safety Concerns: As workplace safety regulations become increasingly stringent, companies are investing in robots to perform inspections in environments that pose risks to human workers.
- Cost Pressures: Facing economic uncertainties, organizations are looking to reduce operational costs while maintaining or improving inspection quality.
- Aging Infrastructure: In many developed countries, critical infrastructure is reaching the end of its designed lifespan, creating an urgent need for more frequent and thorough inspections.
- Technological Advancements: Breakthroughs in AI, sensors, and robotics have made inspection robots more capable, reliable, and cost-effective than ever before.
Types of Inspection Robots
The field of inspection robotics is diverse, with specialized machines designed for specific environments and applications. Let’s explore the major categories:
Aerial Inspection Robots (Drones)
Drones have revolutionized inspection capabilities for tall structures, large areas, and inaccessible locations. These flying robots typically feature:
- Versatile Mobility: The ability to access elevated areas like towers, bridges, and rooftops without scaffolding or climbing equipment.
- High-Resolution Imaging: Equipped with 4K or even 8K cameras that capture detailed visual data from various angles.
- Thermal Imaging: Many inspection drones incorporate infrared cameras that detect heat signatures, revealing issues like energy loss, electrical hotspots, or structural weaknesses.
- LiDAR Technology: Some advanced models use Light Detection and Ranging technology to create precise 3D maps of structures.
These aerial robots excel at inspecting power lines, wind turbines, solar farms, bridges, and building exteriors—tasks that would otherwise require workers to operate at dangerous heights.
Crawler and Wheeled Inspection Robots
These ground-based robots are designed to move across surfaces and through confined spaces:
- Magnetic Crawlers: Robots that use magnetic adhesion to traverse metal surfaces, such as ship hulls, storage tanks, and pipelines.
- Pipe Inspection Robots: Cylindrical robots that travel through pipelines, detecting corrosion, cracks, or blockages.
- Tracked Vehicles: Robust robots with tank-like treads that can navigate rough terrain, debris, and challenging industrial environments.
Crawler robots are particularly valuable for inspecting confined spaces where human entry would require extensive safety measures or might be impossible altogether.
Underwater Inspection Robots (ROVs and AUVs)
Submersible robots have transformed underwater inspection capabilities:
- Remotely Operated Vehicles (ROVs): Tethered underwater robots controlled by operators on the surface, often used for detailed inspections of underwater structures.
- Autonomous Underwater Vehicles (AUVs): Self-guided underwater robots that follow pre-programmed paths or adapt to environmental conditions, ideal for mapping large underwater areas.
These aquatic robots inspect ship hulls, offshore platforms, underwater pipelines, dams, and other submerged infrastructure—environments that would require professional divers working in hazardous conditions.
Humanoid Inspection Robots
Some of the most advanced inspection robots take a humanoid form, designed to navigate environments built for humans:
- Bipedal Movement: These robots walk on two legs, allowing them to climb stairs, step over obstacles, and access areas designed for human workers.
- Articulated Arms: Many humanoid robots feature dexterous arms and hands that can manipulate objects, open doors, or operate controls.
- Human-Like Sensors: They often incorporate vision systems positioned at human eye level, providing familiar perspectives for remote operators.
While less common than other types, humanoid inspection robots excel in complex built environments like nuclear facilities, where they can perform tasks in areas too dangerous for human entry.
Key Industries Transformed by Inspection Robots
Inspection robots are making significant impacts across numerous sectors:
Oil and Gas Industry
The oil and gas sector was among the earliest adopters of inspection robotics, using them to:
- Inspect offshore platforms and subsea infrastructure
- Monitor pipelines for corrosion, leaks, or structural issues
- Examine storage tanks for integrity without emptying them
- Detect gas leaks in processing facilities
These applications have reduced operational downtime, improved safety, and minimized environmental risks in this high-stakes industry.
Power Generation and Utilities
Utility companies increasingly rely on inspection robots to:
- Assess wind turbine blades for damage without costly crane operations
- Inspect solar farms for damaged panels or connection issues
- Monitor power lines and transmission towers for weather damage
- Examine boilers, cooling towers, and other power plant components
By implementing robotic inspections, power companies have reduced outage times and prevented costly failures.
Manufacturing and Production
In manufacturing environments, inspection robots are revolutionizing quality control:
- Performing consistent, objective visual inspections of finished products
- Conducting in-process quality checks at speeds human inspectors cannot match
- Detecting microscopic defects using specialized sensors and imaging technology
- Measuring dimensions with sub-millimeter precision
The result is higher product quality, reduced wastage, and more efficient production processes.
Infrastructure and Construction
Critical infrastructure benefits enormously from robotic inspection:
- Bridge inspections that once required lane closures and put workers at risk
- Sewer and drainage system assessments without confined space entry
- Building façade examinations that previously required expensive scaffolding
- Tunnel inspections that can proceed without traffic disruption
These applications help maintenance teams identify issues before they become critical, extending infrastructure lifespan and improving public safety.
Aerospace and Aviation
Aircraft maintenance has been transformed by inspection robots that:
- Scan aircraft exteriors for damage, missing fasteners, or other issues
- Inspect fuel tanks and other confined spaces without human entry
- Check engine components for wear or damage with precision imaging
- Evaluate composite structures using specialized non-destructive testing techniques
These robotic inspections reduce aircraft downtime and enhance safety through more thorough and consistent checks.
Benefits of Implementing Inspection Robots
Organizations that adopt inspection robots typically realize several significant advantages:
Enhanced Safety
The most compelling benefit is the reduction in workplace hazards:
- Eliminating the need for workers to enter confined spaces
- Reducing work at height requirements
- Minimizing exposure to hazardous substances or environments
- Decreasing physical strain and associated injuries
By keeping human workers out of dangerous situations, inspection robots directly contribute to reduced accident rates and improved workplace safety.
Improved Inspection Quality
Robotic inspections offer unprecedented consistency and detail:
- Eliminating human fatigue factors that can cause missed defects
- Providing quantitative measurements rather than subjective assessments
- Creating comprehensive digital records of every inspection
- Detecting issues invisible to the human eye through specialized sensors
The result is more reliable inspection data and fewer missed defects that could lead to failures or accidents.
Cost Efficiency
Despite the initial investment, inspection robots typically deliver compelling ROI through:
- Reduced labor costs for routine inspections
- Decreased downtime for inspection activities
- Lower insurance premiums due to improved safety records
- Extended asset lifecycles through early detection of issues
Many organizations report that their robotic inspection programs paid for themselves within 12-18 months of implementation.
Accessibility to Hard-to-Reach Areas
Inspection robots excel at accessing areas that are difficult or impossible for human inspectors:
- Confined spaces like tanks, pipes, and ducts
- Elevated structures like towers, bridges, and rooftops
- Submerged assets like underwater pipelines or dam foundations
- Hazardous environments with extreme temperatures or toxic atmospheres
This accessibility enables more comprehensive inspections and eliminates the need for extensive temporary access equipment.
Data-Driven Decision Making
Perhaps the most transformative benefit is the wealth of data these robots generate:
- Creating digital twins of physical assets through 3D mapping
- Enabling trend analysis across multiple inspection cycles
- Supporting predictive maintenance rather than reactive repairs
- Providing objective evidence for regulatory compliance
This data-rich approach transforms inspection from a periodic obligation into a strategic asset management tool.
Challenges and Limitations of Inspection Robots
Despite their impressive capabilities, inspection robots do face several challenges:
Technical Limitations
Current robotic technology has certain constraints:
- Battery life limitations that restrict operational time
- Connectivity issues in remote or shielded environments
- Sensor limitations in certain lighting or environmental conditions
- Mobility challenges in highly complex or unstructured environments
These limitations often require operational adaptations or hybrid approaches combining robotic and human inspection elements.
Implementation Costs
The financial barriers to adoption can be significant:
- High initial investment for robot acquisition
- Training costs for operators and maintenance personnel
- Infrastructure modifications to support robotic operations
- Software and data management system requirements
While costs are decreasing as the technology matures, budget constraints remain a significant adoption barrier for many organizations.
Regulatory and Compliance Considerations
Inspection robots operate in a complex regulatory landscape:
- Some industries have not yet updated standards to accommodate robotic inspections
- Certain regulatory requirements still explicitly require human visual inspection
- Liability questions around robotic inspection reliability remain unresolved
- Privacy concerns arise when robots collect data in public or sensitive areas
Organizations must navigate these regulatory challenges while working with authorities to develop appropriate frameworks for robotic inspections.
Workforce Impact and Resistance
The human dimension of implementation can be challenging:
- Potential workforce concerns about job displacement
- Resistance to changing established inspection procedures
- Learning curve for operators transitioning to robotic systems
- Need for new skills in data analysis and robot maintenance
Successful implementation requires thoughtful change management and workforce development strategies.
How to Implement Inspection Robots in Your Operations
If you’re considering adopting inspection robots, follow these key steps:
Assess Your Needs and Opportunities
Start with a comprehensive evaluation:
- Identify high-risk inspection tasks that could be made safer
- Determine inspection activities that currently cause operational disruptions
- Evaluate areas where inspection quality or consistency could be improved
- Consider regulatory requirements that might affect implementation
This assessment will help prioritize applications where robots can deliver the greatest value.
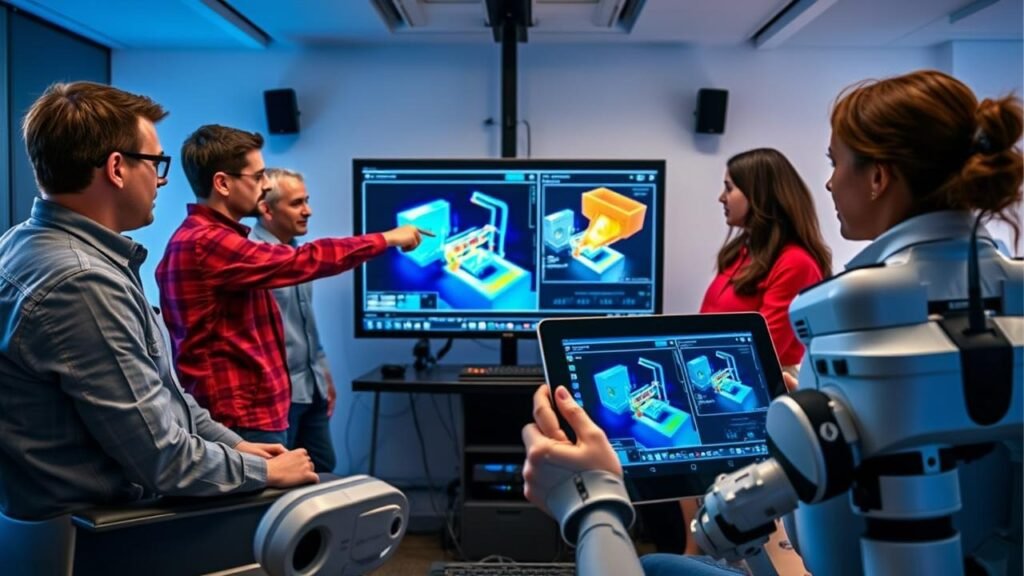
Choose the Right Technology
Select robotic systems suited to your specific requirements:
- Match robot capabilities to your inspection environment
- Consider whether you need customized solutions or off-the-shelf options
- Evaluate integration with existing systems and workflows
- Assess vendor support capabilities and service networks
Remember that the lowest-cost option isn’t always the most economical in the long run.
Develop Implementation Strategies
Plan carefully for successful deployment:
- Create a phased implementation approach starting with high-value applications
- Develop training programs for operators and maintenance personnel
- Establish clear procedures for data collection, analysis, and reporting
- Design contingency plans for situations where robots might not be suitable
Thoughtful planning will minimize disruption and accelerate the realization of benefits.
Measure Results and Optimize
Continuously evaluate and improve your robotic inspection program:
- Track safety improvements, cost savings, and inspection quality metrics
- Gather feedback from operators and stakeholders
- Benchmark against industry standards and best practices
- Regularly update systems and approaches as technology evolves
This continuous improvement approach will maximize the return on your investment.
The Future of Inspection Robots
The inspection robotics field is evolving rapidly, with several emerging trends:
AI and Machine Learning Integration
Artificial intelligence is transforming inspection capabilities:
- Self-learning systems that improve detection accuracy over time
- Predictive analytics that forecast potential failures before they occur
- Autonomous decision-making capabilities for complex inspection scenarios
- Natural language processing for more intuitive human-robot interaction
These AI enhancements will make inspection robots increasingly valuable as strategic assets.
Swarm Robotics and Collaboration
Multiple robots working together represent the next frontier:
- Coordinated inspection of large facilities by robot teams
- Different robot types collaborating to overcome individual limitations
- Complementary sensor capabilities combining to create comprehensive assessments
- Faster inspection of large areas through parallel operations
These collaborative approaches promise dramatic improvements in efficiency and effectiveness.
Enhanced Mobility and Manipulation
Physical capabilities continue to advance:
- Improved battery technology extending operational range
- More versatile locomotion systems for challenging environments
- Advanced manipulation capabilities for interacting with the environment
- Self-recovery features for overcoming obstacles or issues
These enhancements will expand the range of applications where robots can replace hazardous human inspections.
Integrated Inspection and Maintenance
The boundaries between inspection and repair are blurring:
- Robots that can both detect and immediately repair minor issues
- Integrated systems that coordinate inspection robots with maintenance teams
- Predictive maintenance platforms that automatically schedule interventions
- Digital workflows that seamlessly connect inspection findings to work orders
This integration promises to close the loop between finding problems and fixing them.
Case Studies: Inspection Robots in Action
Power Plant Boiler Inspection
A major power utility implemented crawler robots to inspect boiler interiors during scheduled outages:
- Challenge: Traditionally, human inspectors required extensive scaffolding and cooling periods, resulting in lengthy downtime.
- Solution: Heat-resistant crawler robots equipped with HD cameras and ultrasonic thickness sensors.
- Results: Inspection time reduced from five days to eight hours, saving approximately $200,000 per outage in lost generation capacity.
Offshore Oil Platform Inspection
An international oil company deployed underwater ROVs for routine platform inspections:
- Challenge: Diver-based inspections were hazardous, weather-dependent, and required extensive safety protocols.
- Solution: ROVs equipped with multiple cameras, sonar, and cathodic protection measurement tools.
- Results: 85% reduction in diving operations, improved inspection consistency, and the ability to inspect during adverse weather conditions.
Aircraft Maintenance Revolution
A major airline implemented automated drone inspections for lightning strike assessments:
- Challenge: Traditional visual inspections required extensive time and often missed subtle damage.
- Solution: Automated drone system with pre-programmed flight paths and specialized imaging technology.
- Results: Inspection time reduced from 8 hours to 1 hour, with a 28% improvement in detection of subtle damage patterns.
Bridge Infrastructure Monitoring
A state transportation department adopted a multi-robot approach to bridge inspections:
- Challenge: Aging infrastructure required more frequent inspections, straining budgets and causing traffic disruptions.
- Solution: Combination of drones for deck and superstructure inspection and crawler robots for underside assessment.
- Results: 60% cost reduction compared to traditional methods, with the ability to inspect bridges without lane closures.
How to Select the Right Inspection Robot for Your Needs
Choosing the appropriate inspection robot requires careful consideration of several factors:
Environment and Application Requirements
Assess the specific conditions where the robot will operate:
- Temperature extremes that might affect battery life or electronics
- Presence of flammable gases requiring intrinsically safe designs
- Space constraints that limit robot size or mobility options
- Surface conditions that affect traction or adhesion capabilities
Match these environmental factors to robot specifications to ensure reliable operation.
Sensor and Data Collection Needs
Determine what information you need to gather:
- Visual inspection requirements (resolution, lighting conditions, angles)
- Need for specialized sensing (thermal, ultrasonic, radiographic)
- Data format compatibility with your analysis systems
- Real-time monitoring versus data collection for later analysis
The right sensors will determine the value of the inspection data collected.
Operational Considerations
Evaluate how the robot will fit into your workflows:
- Ease of deployment and retrieval
- Training requirements for operators
- Battery life and charging infrastructure
- Maintenance needs and spare parts availability
These practical factors often determine the success of robotic inspection programs.
Budget and ROI Expectations
Develop a comprehensive financial model:
- Initial acquisition costs versus operational savings
- Expected lifespan and maintenance expenses
- Training and implementation costs
- Potential savings from improved inspection quality
A thorough ROI analysis will help justify the investment and select the most cost-effective solution.
Frequently Asked Questions About Inspection Robots
How much do inspection robots typically cost?
Inspection robot costs vary dramatically based on type, capabilities, and applications:
- Basic inspection drones start around $5,000 but can exceed $50,000 for specialized industrial models
- Crawler robots typically range from $20,000 to $100,000 depending on capabilities
- Underwater ROVs can cost between $30,000 and $500,000
- Custom solutions for specialized environments can exceed $1 million
Most organizations find that leasing options or inspection-as-a-service models offer more flexibility for initial implementation.
Do inspection robots require specialized operators?
The level of operator expertise required depends on the robot type and application:
- Basic inspection drones can be operated by personnel with minimal training (1-2 days)
- Complex ROVs typically require certified operators with extensive training
- Autonomous systems require less operational expertise but more data analysis skills
- Maintenance often requires specialized technical knowledge regardless of robot type
Most vendors offer training programs as part of their implementation packages.
Can inspection robots completely replace human inspectors?
While robots excel at many inspection tasks, complete replacement of human inspectors is rare:
- Robots excel at gathering objective data but may miss contextual insights
- Some regulatory frameworks still require human verification
- Complex judgment calls often benefit from human expertise
- Unusual or unexpected conditions may require human problem-solving
The most effective approach typically combines robotic data collection with human analysis and decision-making.
How do inspection robots handle data security concerns?
Data security has become a critical consideration for industrial inspection robots:
- Many systems now feature encrypted data transmission
- On-device processing can minimize sensitive data transmission
- Access controls limit who can view or download inspection results
- Geo-fencing features can prevent data collection in unauthorized areas
Organizations should include IT security teams in robot selection and implementation planning.
What maintenance do inspection robots require?
Maintenance requirements vary by robot type but typically include:
- Regular battery replacement or reconditioning
- Sensor calibration and cleaning
- Software updates and security patches
- Physical wear component replacement (treads, propellers, etc.)
Most manufacturers recommend preventive maintenance schedules based on operating hours or cycles.
Conclusion
Inspection robots represent one of the most significant safety and efficiency advancements in industrial operations in recent decades. By removing humans from hazardous environments while improving inspection quality and consistency, these technological marvels are transforming how organizations maintain critical infrastructure and ensure operational reliability.
As you consider implementing inspection robots in your operations, remember that successful adoption requires thoughtful planning, appropriate technology selection, and a commitment to continuous improvement. The initial investment—both financial and organizational—can deliver substantial returns through enhanced safety, improved inspection quality, and reduced operational disruptions.
The field of inspection robotics continues to evolve rapidly, with advances in artificial intelligence, sensor technology, and physical capabilities expanding the range of applications where robots can deliver value. Organizations that embrace these technologies today will be well-positioned to benefit from future advancements and maintain competitive advantages in their industries.
Are you ready to explore how inspection robots might transform your operations? Consider starting with a pilot project focused on high-value applications, and build from there as you develop expertise and confidence in this transformative technology.
Further Reading and Resources
For more information on inspection robots and related technologies, consider these authoritative resources:
- American Society for Nondestructive Testing (ASNT) – Resources on robotic inspection standards and certifications
- Robotics Industry Association (RIA) – Industry insights and safety standards for robotic systems
- Institute of Electrical and Electronics Engineers (IEEE) Robotics and Automation Society – Research and technical standards
- International Federation of Robotics (IFR) – Global statistics and trends in industrial robotics
- U.S. Department of Energy Robotics Program – Information on robotics for hazardous environments